Understanding the Manufacturing Process of Epoxy Resins
Written by: Vertec BioSolvents
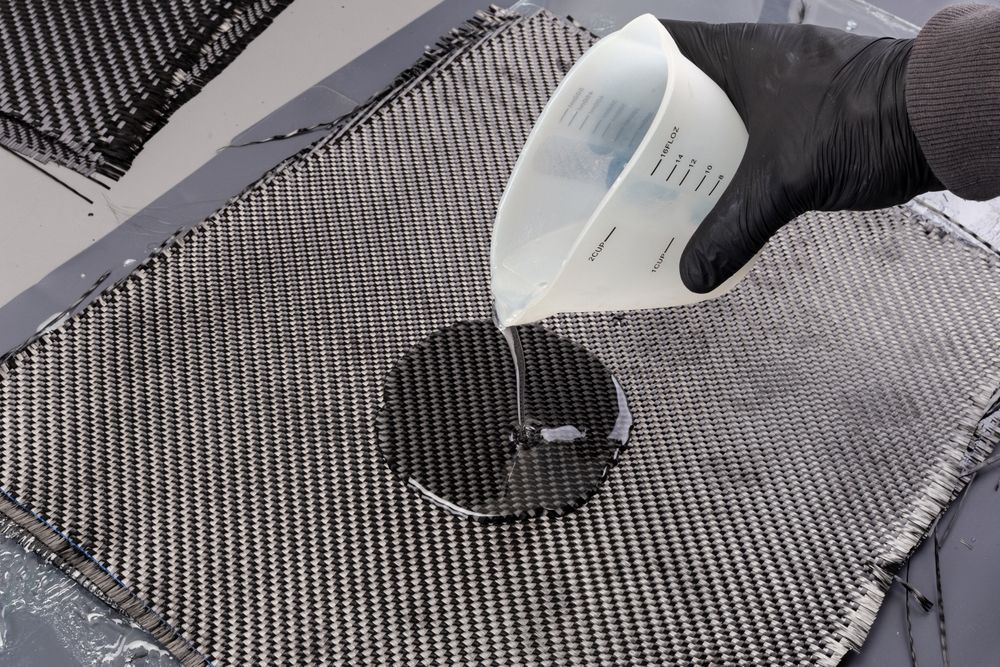
Epoxy resins are used across a wide range of industries for their strength, durability, and resistance to heat and chemicals. Found in everything from industrial coatings and adhesives to electronics and composite materials, these polymers are valued for their high performance in demanding environments.
The production of epoxy resin involves several carefully controlled steps that transform raw materials into a finished product. Understanding what epoxy resins are made of, how they are manufactured, and the environmental impact of that process is key to improving both performance and sustainability.
What Is Epoxy Resin Made Of?
Epoxy resin is primarily made from two key components: epichlorohydrin and bisphenol-A (BPA). These two substances undergo a chemical reaction to form a liquid or solid resin base, depending on the desired end use. Epichlorohydrin is typically derived from petrochemical sources, while BPA is a synthetic compound made from acetone and phenol.
In addition to these base ingredients, epoxy resin formulations may include modifiers, reactive diluents, stabilizers, and other additives to fine-tune performance. These adjustments affect properties such as flexibility, curing speed, viscosity, and resistance to heat or chemicals.
The combination of these components creates a versatile material that can be customized for applications ranging from high-strength adhesives to corrosion-resistant coatings.
Understanding the Epoxy Manufacturing Process
The epoxy manufacturing process involves several tightly controlled steps to ensure product consistency and performance. From raw material preparation to final curing, each phase must meet specific technical and safety standards.
Key stages include the synthesis of the resin, blending with hardeners and additives, controlled curing, and rigorous quality control. Factors such as temperature, mixing ratios, and reaction time directly influence the strength, flexibility, and chemical resistance of the final product.
Understanding each stage is essential for manufacturers looking to optimize epoxy performance across various industrial applications.
Synthesis of Epoxy Resins
Epoxy resin synthesis begins with a chemical reaction between epichlorohydrin and bisphenol-A (BPA) in the presence of a base such as sodium hydroxide. This reaction produces glycidyl ethers, which contain the reactive epoxy groups responsible for the material’s strength and durability.
The resin can be tailored to different viscosities and molecular weights depending on the application. Lower molecular weight resins are commonly used in coatings and adhesives, while higher molecular weight versions are preferred for structural and composite uses.
Blending with Hardener
After synthesis, epoxy resin is combined with a hardener to initiate the curing process. Hardeners, also known as curing agents, are typically amines or anhydrides that react with the epoxy groups to form a solid, cross-linked structure.
The ratio of resin to hardener is carefully calculated to achieve proper curing. An incorrect mix can result in poor mechanical strength, incomplete curing, or surface defects. Additives such as fillers, pigments, or flexibilizers may also be introduced at this stage to modify performance characteristics like color, viscosity, or impact resistance.
Curing and Setting
Curing is the chemical process that transforms liquid epoxy into a solid, cross-linked material. Once the resin and hardener are blended, the mixture begins to react and gradually hardens. This reaction can be accelerated with heat or controlled through ambient curing, depending on the formulation.
The curing phase determines the final mechanical and chemical properties of the epoxy, including hardness, flexibility, and resistance to heat or corrosion. In industrial settings, precise control over time and temperature during this stage is important for achieving consistent results.
Quality Control
Throughout epoxy resin manufacturing, quality control is essential to ensure the final product meets performance and safety standards. Testing begins with raw materials and continues through synthesis, blending, and curing.
Key tests evaluate viscosity, reactivity, hardness, adhesion, and chemical resistance. Other assessments may include thermal stability, pot life, and appearance. These checks help identify inconsistencies, prevent defects, and maintain compliance with industry specifications.
Addressing Environmental Impact of Epoxy Resin Manufacturing
Traditional epoxy resin manufacturing relies heavily on petroleum-based inputs and chemical processes that can release volatile organic compounds (VOCs) and hazardous byproducts. These emissions contribute to air pollution, create health risks in production environments, and increase regulatory pressure on manufacturers.
Waste generated during synthesis, blending, and cleanup is also difficult to manage. Thermoset resins cannot be remelted or easily recycled, leading to long-term disposal challenges.
As sustainability becomes a priority across industries, reducing emissions, improving worker safety, and minimizing waste are key goals for resin producers looking to lower their environmental footprint.
Sustainable Alternatives and Renewable Solutions
Reducing the environmental impact of epoxy resin production starts with using renewable materials and cleaner processing methods. Bio-based resins made from natural sources like plant oils and lignin are gaining traction as alternatives to petroleum-based systems.
Waterborne and low-VOC formulations also help reduce emissions during application and cleanup. These innovations support more sustainable manufacturing without sacrificing essential performance.
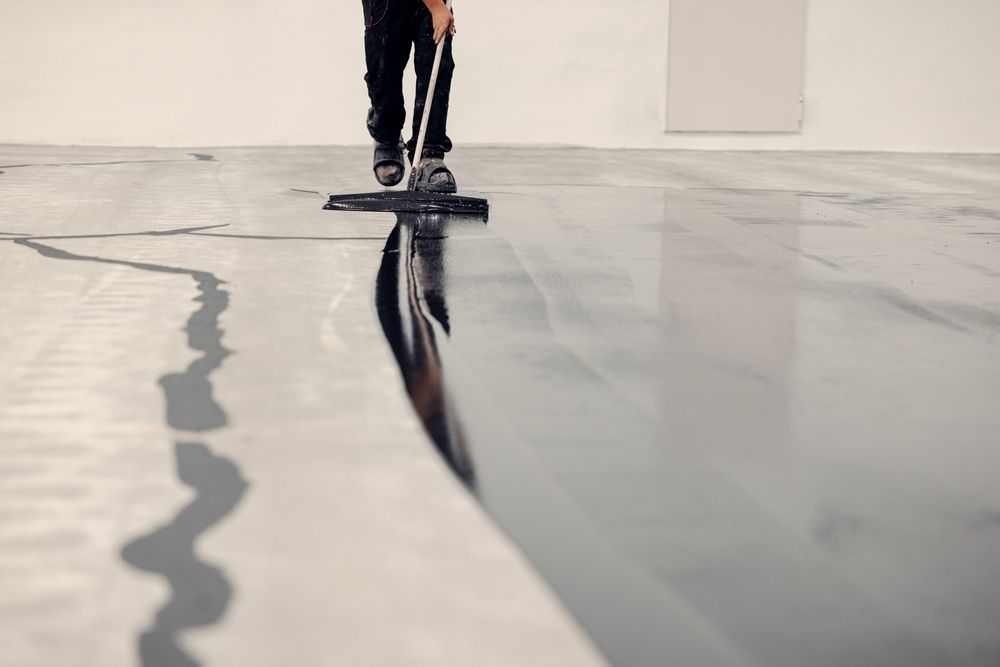
Bio-Based Solvents: A Smarter Choice for Epoxy Resin Production
Solvents are often used during epoxy resin formulation, application, and equipment cleanup. Traditional petroleum-based solvents can release high levels of VOCs, contributing to air pollution and creating safety risks in the workplace.
Bio-based solvents offer a cleaner, safer alternative. Derived from renewable sources like corn, soy, or citrus, these solvents reduce harmful emissions while maintaining the performance needed for industrial use. They are compatible with many epoxy systems and can be integrated with minimal changes to process or equipment.
Switching to bio-based solvents is a practical step toward more sustainable epoxy resin manufacturing and improved regulatory compliance.
Choose Vertec BioSolvents for Sustainable Epoxy Resin Formulations
Vertec BioSolvents provides high-performance, renewable solvent solutions that help manufacturers reduce the environmental impact of epoxy resin production. Made from bio-based sources like corn and soy, these solvents offer a safer alternative to traditional petroleum-based chemicals used in formulation, processing, and cleanup.
With low VOC emissions and strong compatibility with epoxy systems, Vertec’s products support cleaner operations, improved worker safety, and compliance with environmental regulations. Manufacturers can integrate these solvents without sacrificing performance or process efficiency.
To learn how
Vertec BioSolvents can support your sustainability goals,
contact our team for customized recommendations and technical support.