Types of Industrial Resins and How They Are Used
Written by: Vertec BioSolvents
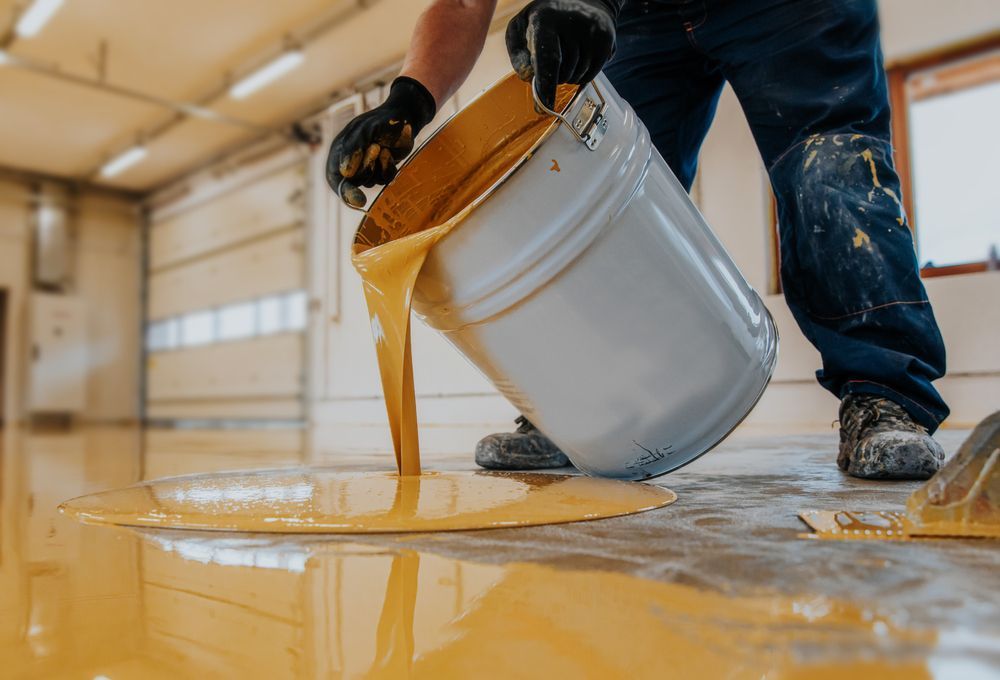
Industrial resins are essential to modern manufacturing, providing strength, flexibility, adhesion, and chemical resistance across a wide range of applications. From protective coatings and automotive parts to electronics and construction materials, these compounds are engineered for high performance in demanding environments.
Many traditional resins are petroleum-based and rely on harsh solvents during processing, raising concerns about safety, emissions, and environmental impact. As industries move toward more sustainable practices, the demand for safer, high-performance alternatives continues to grow.
Vertec BioSolvents supports this transition with bio-based solvent solutions that reduce hazardous emissions and improve the sustainability of resin systems without compromising performance or reliability.
What Are Industrial Resins?
Industrial resins are polymer-based compounds used to bond, coat, or reinforce materials in manufacturing. Designed for strength, durability, and chemical resistance, they play a critical role in industries like construction, automotive, electronics, and aerospace. Most are either thermosetting or thermoplastic and can be engineered to meet specific performance requirements.
Different Types of Industrial Resins and Their Applications
The performance and characteristics of an industrial resin depend largely on its chemical structure and formulation. Some resins offer excellent thermal resistance, while others are valued for flexibility, adhesion, or fast curing times. Choosing the right resin depends on the intended application, environmental exposure, and required mechanical properties.
Epoxy Resin
Epoxy resins are high-performance thermosets known for strong adhesion, chemical resistance, and durability. They’re used in coatings, adhesives, composites, and electronic components.
Common Uses:
- Protective coatings for concrete, steel, and marine equipment
- Structural adhesives in automotive and aerospace
- Electrical insulation and circuit boards
Pros:
- Excellent strength and chemical resistance
- Strong substrate adhesion
- Low shrinkage during cure
Cons:
- Can be brittle without proper formulation
- Petroleum-based with VOC concerns
- Requires precise handling and curing
Polyester Resin
Polyester resins are versatile, cost-effective thermosets commonly used in fiberglass-reinforced plastics, marine components, automotive parts, and construction materials. Known for fast curing and good mechanical properties, they’re widely adopted in high-volume applications.
Common Uses:
- Fiberglass moldings and panels
- Boat hulls and marine composites
- Automotive body parts and structural panels
- Concrete repair and construction materials
Pros:
- Low cost and easy processing
- Fast curing times
- Good mechanical strength and dimensional stability
Cons:
- Lower chemical and UV resistance compared to epoxies
- Strong odor and high VOC emissions
- Less durable in highly corrosive environments
Acrylic Resins
Acrylic resins are known for their clarity, UV resistance, and weatherability. Available in both thermoplastic and thermosetting forms, they are widely used in coatings, adhesives, sealants, and plastic parts where color retention and environmental durability are key.
Common Uses:
- Architectural and automotive coatings
- Sealants and adhesives
- Plastics, signage, and display materials
- Protective finishes for wood, metal, and concrete
Pros:
- Excellent UV and weather resistance
- Good color and gloss retention
- Fast drying and easy application
Cons:
- Lower chemical and heat resistance than epoxy or polyurethane
- Can be brittle in high-impact applications
- Often requires solvents that emit VOCs
Polyurethane Resin
Polyurethane resins are highly adaptable polymers valued for their toughness, flexibility, and abrasion resistance. They can be formulated as rigid or flexible foams, elastomers, coatings, and adhesives, making them suitable for a wide range of industrial applications.
Common Uses:
- Protective coatings and floor finishes
- Sealants and adhesives
- Foam insulation and cushioning materials
- Automotive interior parts and components
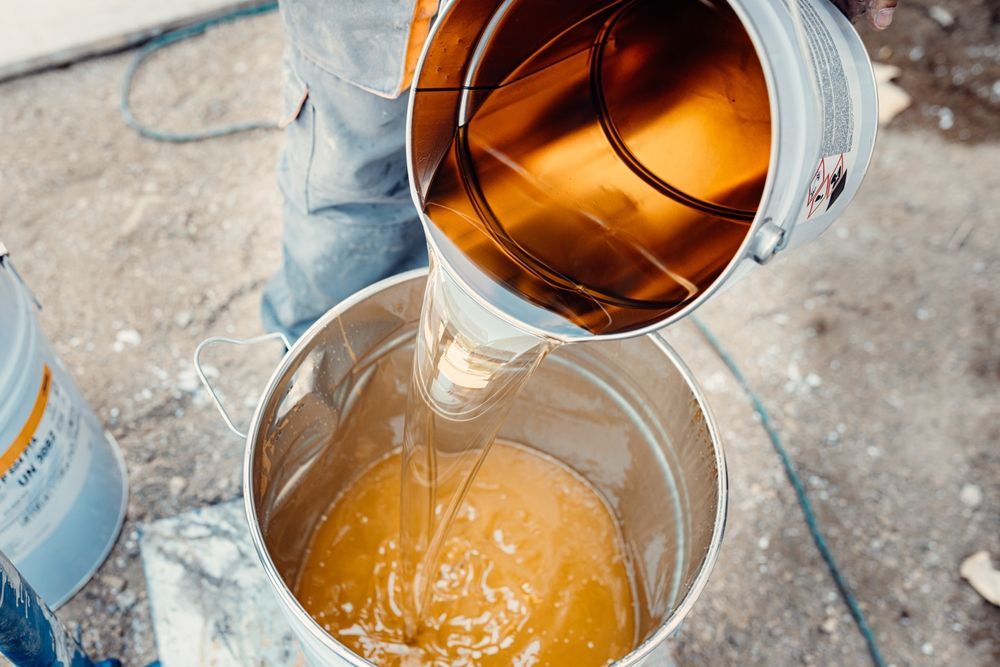
Pros:
- Excellent flexibility and impact resistance
- Strong adhesion to various substrates
- Resistant to abrasion, oils, and chemicals
Cons:
- Sensitivity to moisture during curing
- Can emit hazardous isocyanates during processing
- Often relies on petroleum-based inputs and solvents
Isocyanate Resins
Isocyanate resins are reactive components used in the production of polyurethane systems. When combined with polyols, they form rigid or flexible foams, coatings, adhesives, and elastomers. These resins offer high performance but are tightly regulated due to their toxicity and health risks during processing.
Common Uses:
- Two-component polyurethane coatings
- Rigid and spray foams for insulation
- High-performance adhesives and sealants
- Industrial elastomers and molded parts
Pros:
- High strength and durability
- Fast reactivity and curing times
- Excellent chemical and abrasion resistance
Cons:
- Toxic vapor exposure risk during application
- Strict handling and PPE requirements
- Environmental and regulatory concerns
Polyamide Polymers
Polyamide polymers, including both thermoplastic nylons and reactive polyamide resins, are valued for their strength, toughness, and resistance to abrasion and chemicals. They’re used in everything from structural components to hot-melt adhesives and high-performance coatings.
Common Uses:
- Engineering plastics and molded parts
- Hot-melt and pressure-sensitive adhesives
- Flexible packaging and films
- Industrial coatings and primers
Pros:
- Excellent mechanical and thermal properties
- Good resistance to oils, fuels, and solvents
- Strong adhesion and flexibility in coatings
Cons:
- Sensitive to moisture absorption
- Higher processing temperatures required
- Some types rely on petrochemical feedstocks
Melamine Polymers
Melamine resins are thermosetting polymers formed by reacting melamine with formaldehyde. Known for their hardness, heat resistance, and glossy finish, they are commonly used in laminates, coatings, and molded products.
Common Uses:
- Decorative laminates (e.g., countertops, flooring)
- Heat-resistant coatings and finishes
- Molded kitchenware and electrical components
- Paper and textile treatments
Pros:
- High hardness and heat resistance
- Excellent surface durability and appearance
- Cost-effective for large-scale applications
Cons:
- Brittle under impact or stress
- Contains formaldehyde, raising health and environmental concerns
- Limited flexibility in formulation
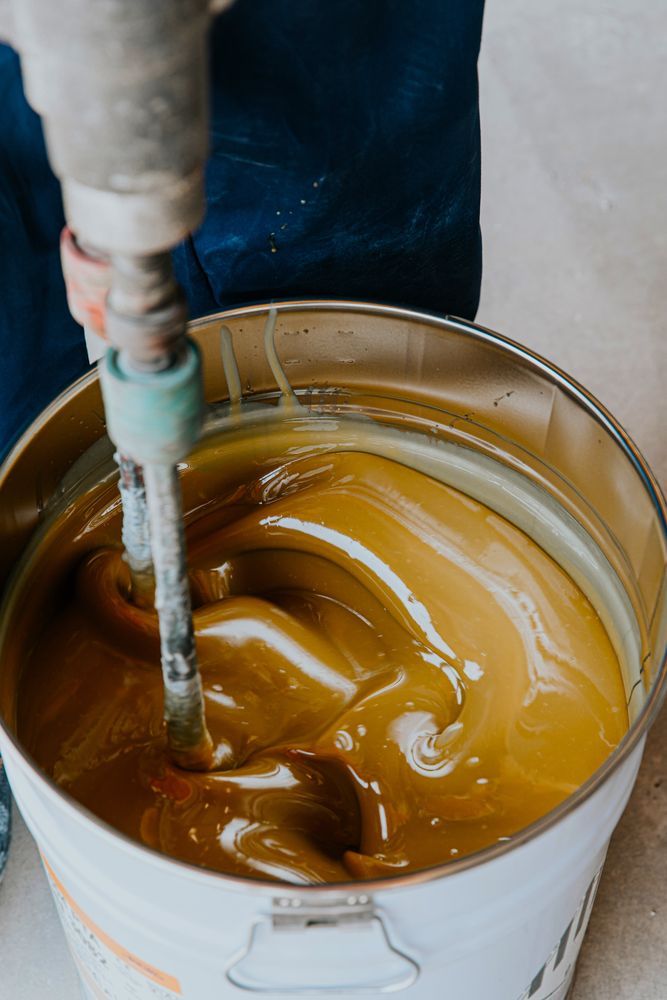
How Are Industrial Resins Formulated and Manufactured?
Industrial resins are produced by chemically reacting monomers to form polymer chains. These monomers are typically sourced from petroleum, though bio-based alternatives are becoming more common. The resulting polymers are then blended with additives such as catalysts, fillers, plasticizers, and stabilizers to achieve specific properties like flexibility, curing speed, or chemical resistance.
Thermosetting resins cure through chemical reactions or heat, forming a rigid, cross-linked structure that cannot be remelted. Thermoplastics, on the other hand, can be softened and reshaped with heat. Manufacturing processes must be carefully controlled to ensure consistency, safety, and performance.
Industrial Resin Waste and Environmental Concerns
Resin production and use can generate significant environmental impacts. VOCs and hazardous air pollutants are often released during manufacturing and application, especially when solvents are involved. Improper disposal of resin waste also poses risks to soil and water quality.
Thermosetting resins are particularly challenging to recycle due to their permanent chemical structure, which leads to more landfill waste. As regulations tighten around emissions and hazardous materials, manufacturers are under increasing pressure to adopt cleaner, safer alternatives.
Sustainable Industrial Resins and Eco-Friendly Alternatives
Sustainable resins aim to reduce environmental impact by replacing petroleum-based ingredients, lowering emissions, and improving recyclability. Bio-based resins derived from renewable sources like soy, corn, and cellulose are being used in coatings, adhesives, and composites.
Low-VOC technologies such as waterborne and high-solids systems are also helping reduce air emissions. Some manufacturers are moving toward recyclable thermoplastics and biodegradable polymers to cut down on waste.
Advancements in formulation have made many of these alternatives competitive in performance, giving manufacturers a practical path toward meeting sustainability goals without sacrificing quality.
How Vertec BioSolvents Supports Sustainable Resin Formulations
Vertec BioSolvents offers renewable, bio-based solvent alternatives that help reduce VOC emissions and environmental impact in resin systems. Made from corn, soy, and citrus, these solvents are used in formulation, application, and cleanup across a wide range of resins, including epoxy, polyurethane, acrylic, and polyester.
These solutions support cleaner production, safer work environments, and compliance with environmental regulations while maintaining the performance and efficiency that manufacturers require.
To explore how Vertec BioSolvents can help improve the sustainability of your resin systems, contact our team to discuss custom solvent solutions tailored to your needs.